Physical Vapor Deposition (PVD) coating represents one of the most advanced surface treatment technologies available today. Moreover, this innovative process transforms how manufacturers enhance product durability and performance. Furthermore, PVD coating provides exceptional protection while maintaining environmental sustainability.
Specifically, PVD coating involves depositing thin films onto various substrates through physical processes. Additionally, this technology operates in vacuum environments, ensuring superior coating quality. Consequently, industries worldwide adopt PVD coating for critical applications requiring enhanced surface properties.
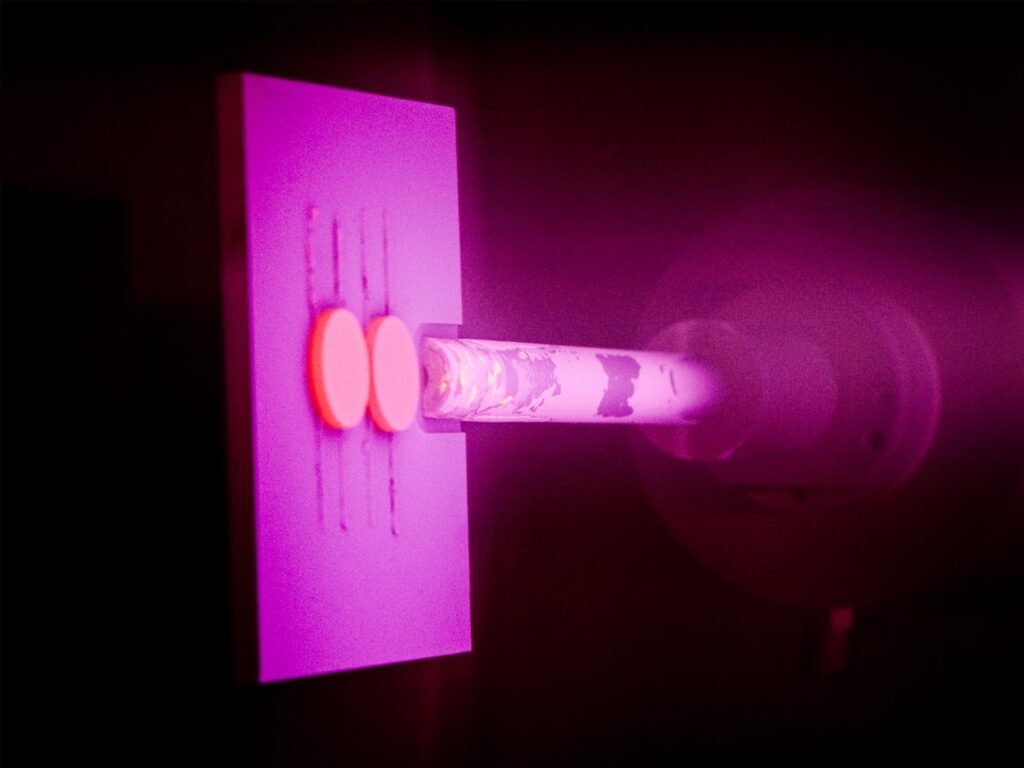
How PVD Coating Works: The Technical Process
The PVD process begins with creating a controlled vacuum environment. Initially, technicians place target materials and substrates into specialized chambers. Subsequently, they remove air and contaminants to achieve optimal vacuum conditions.
Next, the system heats or bombards target materials using various energy sources. For example, electron beams, ions, or thermal energy vaporize solid materials. As a result, these materials transform into gaseous states while maintaining their chemical composition.
Following this, vaporized materials travel through the vacuum chamber toward substrates. Importantly, this journey occurs without chemical reactions or contamination. Finally, these materials condense on substrate surfaces, forming uniform, adherent coatings.
Furthermore, operators can control coating thickness, composition, and properties throughout the process. Therefore, PVD coating delivers precise, repeatable results for demanding applications.
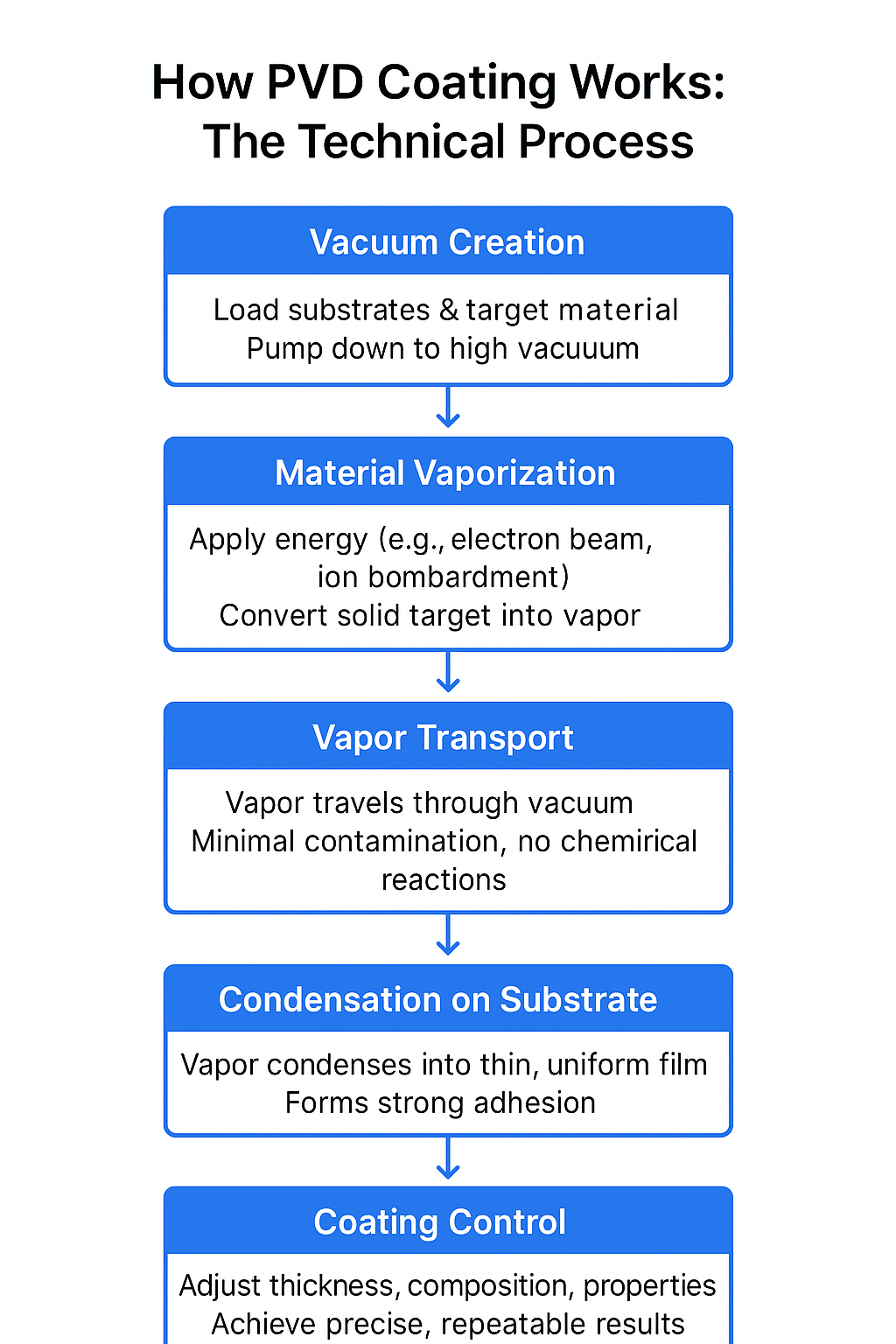
Major Types of PVD Coating Technologies
Sputtering Process
Sputtering represents the most widely used PVD technique. Specifically, this process bombards target materials with energetic ions. Consequently, atoms eject from target surfaces and deposit onto substrates. Moreover, sputtering provides excellent coating uniformity and adhesion.
Evaporation Process
Thermal evaporation uses heat to vaporize coating materials. Additionally, electron beam evaporation offers precise temperature control. Therefore, these methods work exceptionally well for pure metal coatings.
Ion Plating Process
Ion plating combines evaporation with ion bombardment. Furthermore, this technique enhances coating adhesion and density. As a result, ion plating produces superior mechanical properties.
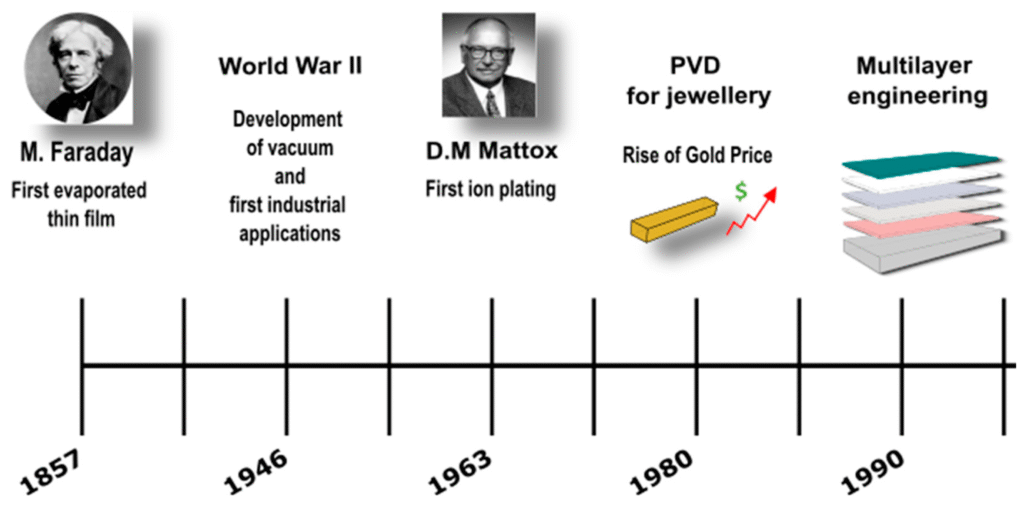
Key Benefits and Advantages of PVD Coating
Enhanced Durability
PVD coatings significantly improve surface hardness and wear resistance. Moreover, these coatings withstand extreme operating conditions effectively. Consequently, products last longer and require less maintenance.
Environmental Advantages
Unlike traditional electroplating, PVD processes generate no toxic waste streams. Additionally, they consume less energy and water. Therefore, PVD coating supports sustainable manufacturing practices.
Superior Performance
PVD coatings offer excellent corrosion resistance and thermal stability. Furthermore, they maintain consistent performance across temperature ranges. Additionally, these coatings provide outstanding electrical and optical properties.
Cost Effectiveness
Initially, PVD coating may seem expensive compared to alternatives. However, the extended product lifespan reduces total ownership costs. Moreover, improved performance often justifies the initial investment.
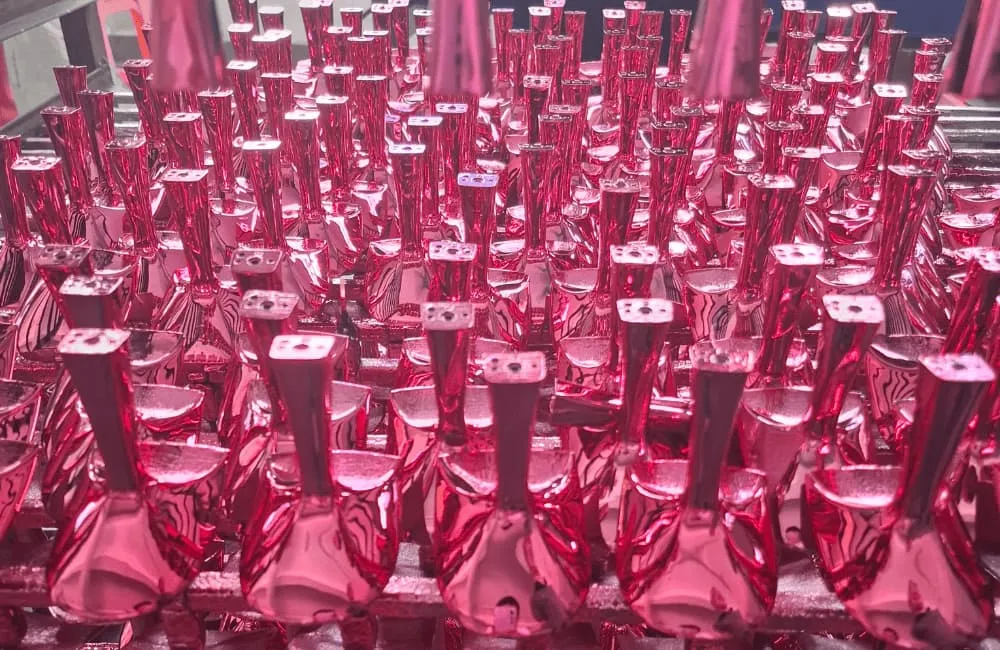
Wide-Ranging Applications of PVD Coating
Automotive Industry
Automotive manufacturers extensively use PVD coating for engine components. Specifically, they apply coatings to pistons, valves, and cutting tools. Furthermore, PVD coating enhances fuel efficiency and reduces emissions.
Aerospace Applications
Aerospace components require exceptional performance under extreme conditions. Moreover, PVD coatings provide necessary protection for turbine blades and structural parts. Additionally, these coatings reduce weight while improving strength.
Medical Device Industry
Medical applications demand biocompatible, corrosion-resistant surfaces. Consequently, PVD coating protects surgical instruments and implants effectively. Furthermore, these coatings maintain sterility and prevent contamination.
Electronics and Semiconductors
Electronic devices benefit from PVD coating’s precise thickness control. Additionally, these coatings provide electrical conductivity or insulation as needed. Therefore, PVD coating enables advanced semiconductor manufacturing.
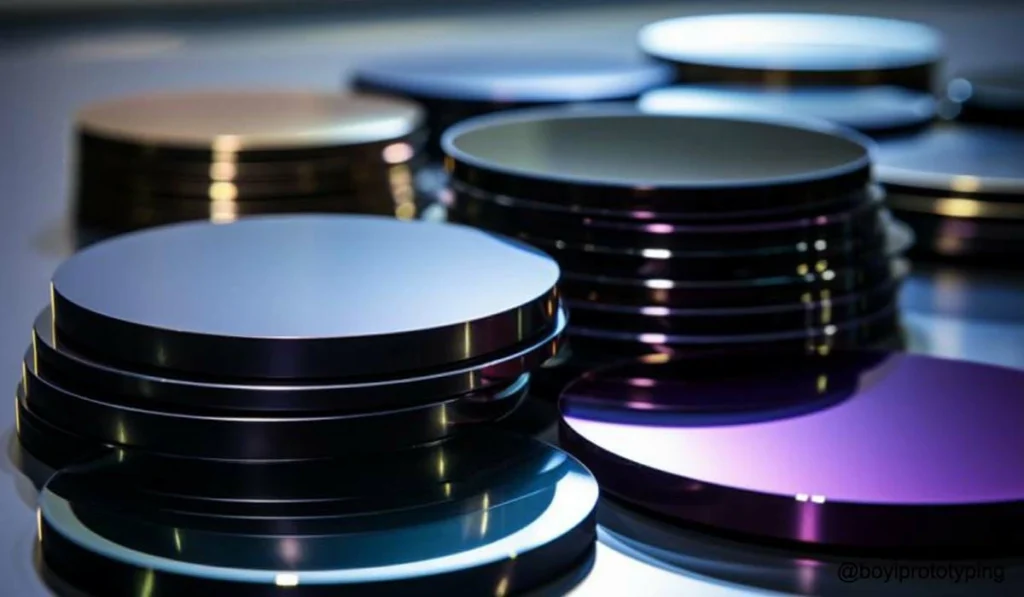
PVD Coating vs Other Surface Treatment Methods
Comparison with Electroplating
Electroplating uses chemical processes in liquid solutions. However, PVD coating operates in vacuum environments without chemicals. Moreover, PVD produces thinner, more uniform coatings with superior properties.
Advantages over CVD Coating
Chemical Vapor Deposition (CVD) requires high temperatures and reactive gases. Conversely, PVD coating operates at lower temperatures with inert environments. Therefore, PVD coating suits temperature-sensitive substrates better.
Benefits vs Traditional Paint
Conventional paints provide limited durability and performance. Furthermore, they often contain volatile organic compounds. In contrast, PVD coating offers superior protection without environmental concerns.
Important Considerations When Choosing PVD Coating
Substrate Compatibility
Different substrates require specific PVD coating approaches. Moreover, surface preparation significantly affects coating adhesion. Therefore, proper substrate analysis ensures optimal results.
Coating Requirements
Performance specifications determine appropriate PVD coating types. Additionally, operating conditions influence coating selection decisions. Consequently, thorough requirement analysis guides proper choices.
Economic Factors
Cost considerations include initial investment and operating expenses. Furthermore, volume requirements affect equipment selection. However, long-term benefits often outweigh initial costs.
Quality Standards
Industry standards specify coating quality requirements. Moreover, certification processes ensure consistent performance. Therefore, selecting qualified PVD coating providers proves essential.
Future Trends and Innovations in PVD Coating
Emerging technologies continue advancing PVD coating capabilities. Moreover, new materials expand application possibilities significantly. Additionally, automation improves process consistency and reduces costs.
Hybrid processes combine PVD with other technologies for enhanced performance. Furthermore, real-time monitoring systems optimize coating quality. Consequently, PVD coating technology evolves to meet changing industry demands.
Environmental regulations drive further PVD coating adoption. Moreover, sustainability requirements favor clean technologies. Therefore, PVD coating represents the future of surface treatment.
Conclusion: The Value of PVD Coating Technology
PVD coating delivers exceptional performance benefits across numerous industries. Moreover, this technology provides environmentally friendly solutions for surface enhancement. Additionally, ongoing innovations continue expanding PVD coating applications.
Manufacturers who embrace PVD coating gain competitive advantages through improved product performance. Furthermore, reduced maintenance costs and extended product life cycles provide substantial economic benefits. Therefore, PVD coating represents a strategic investment in manufacturing excellence.
Finally, understanding PVD coating technology helps businesses make informed decisions about surface treatment options. Moreover, proper implementation ensures maximum return on investment while supporting sustainability goals.
Reference source: DLC Coating: A Comprehensive Guide to Diamond-Like Carbon
External reference sources:https://en.wikipedia.org/wiki/Physical_vapor_deposition